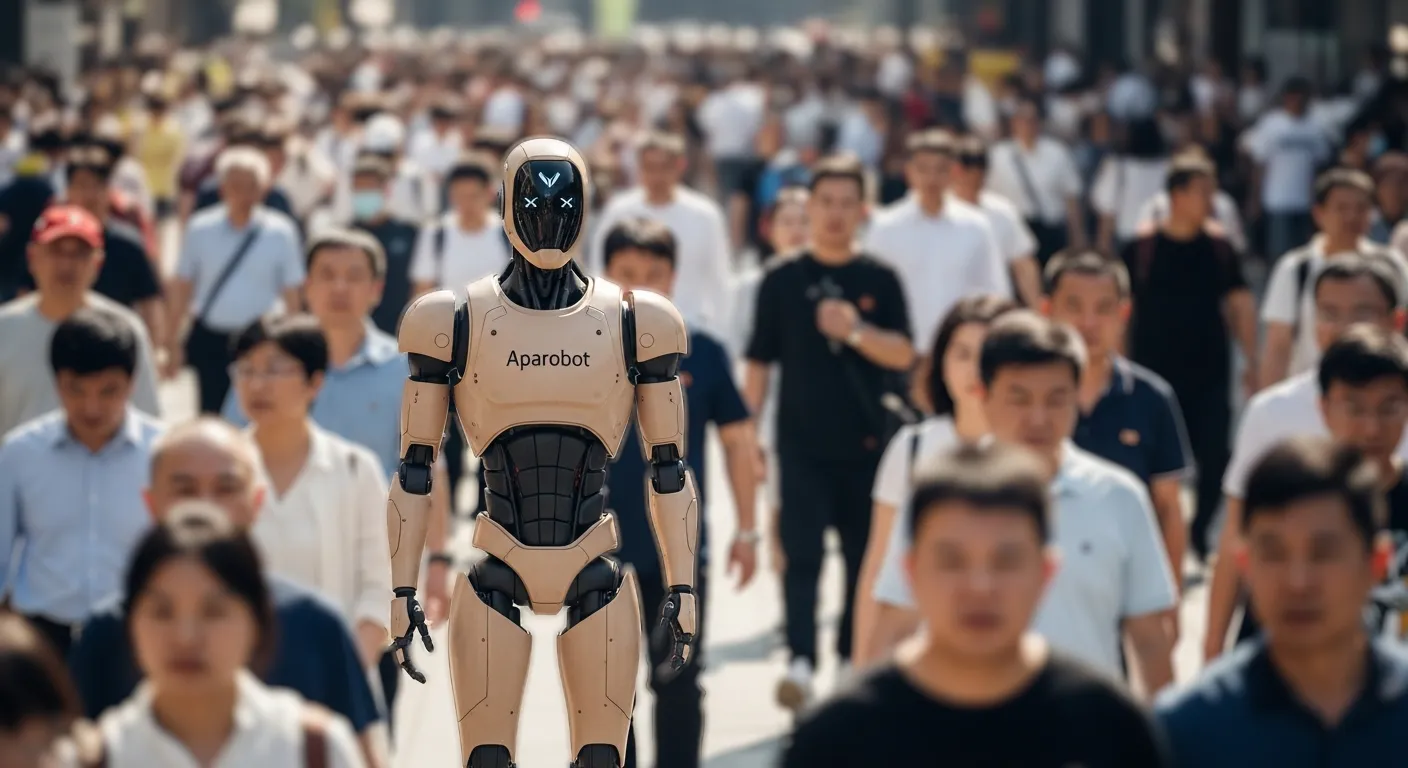
A staggering $46.9 billion flowed into robotics systems across Chinese factories in 2020 – more than the U.S. and EU combined. This explosive growth transformed the nation from a manufacturing underdog to the undisputed automation superpower of the 21st century. While traditional industrial leaders hesitated, China deployed over 339,000 operational units by 2016 alone.
The country now controls 36% of global robotics investments, a strategic move reshaping entire supply chains. From automotive plants to electronics assembly lines, smart machines complete tasks 50% faster than human workers. This shift isn’t just about efficiency – it’s a calculated play to dominate next-gen tech sectors like AI-driven manufacturing.
What makes this transformation remarkable is its speed. In less than a decade, Chinese firms outpaced German engineering and Japanese precision. Government subsidies, tech education programs, and private-sector innovation created a perfect storm. The results? Production lines that adapt in real-time and factories operating with 90% less downtime.
This revolution carries global implications. As Western nations debate automation ethics, China’s tech ecosystem integrates machine learning into every industrial process. The convergence of 5G networks and cloud robotics creates systems that learn from each other nationwide. Tomorrow’s economic battles will be fought not with tariffs, but with self-optimizing assembly robots.
Key Takeaways
- China represents 36% of worldwide robotics spending, triple the U.S. investment
- Operational machine units surpassed 339,000 by 2016, doubling every 3 years
- AI integration boosts production speed by 50% compared to traditional methods
- Next-gen factories achieve 90% operational uptime through adaptive systems
- 5G networks enable real-time coordination between smart manufacturing hubs
Unveiling China's Robotic Industry Transformation
The landscape of industrial production underwent seismic shifts as automated systems replaced traditional assembly lines at unprecedented rates. Between 2012 and 2017, robot production surged 20-fold – from 5,800 units to 131,000 – marking the fastest tech adoption curve in modern manufacturing history.
Demographic pressures accelerated this shift. The working-age population shrank by 4% annually since 2015, creating what analysts call a “labor vacuum” in factories. Our analysis of the CEES survey reveals 68% of 2,000 surveyed firms cite worker shortages as their primary automation driver.
Three sectors dominate robotics integration:
- Electronics assembly (42% adoption rate)
- Automotive manufacturing (37%)
- Industrial machinery (29%)
Local manufacturers capitalized on massive domestic demand, achieving 30% cost reductions through scaled production. This accessibility transformed smaller enterprises – 54% now use basic robotic systems compared to 12% in 2015.
The data paints a clear trajectory: automated solutions aren’t replacing workers but filling critical gaps in an aging workforce. As one Guangzhou factory manager noted, “Our machines work triple shifts without fatigue – something humans haven’t done since 2010.”
Robots in China: Driving Manufacturing, Innovation, and Policy
China's factories now produce more cars than the U.S. and Japan combined. Over 70% of global electronics originate from these facilities. This manufacturing dominance created ideal conditions for automation growth.
The "Made in China 2025" initiative turbocharged this shift. It mandated 150 automated units per 10,000 workers by 2020. State-backed subsidies proved critical – publicly traded firms derive 40% of profits from government support.
Rising labor costs forced strategic changes. Worker shortages grew 4% annually since 2015. "Automation became survival, not choice," explains a Shenzhen factory executive. Manufacturers now deploy robotic solutions to maintain export competitiveness.
Strategic policies built complete production ecosystems. Domestic suppliers now provide 65% of robotic components. This vertical integration slashed costs by 30% since 2018. Global tech leaders face new competition from homegrown innovators.
These coordinated efforts transformed industrial capabilities. Electronics firms achieve 92% production uptime through adaptive systems. Automotive plants reduced assembly errors by 47% using smart machines. The country’s industrial policy framework proves automation success requires more than technology – it demands synchronized economic planning.
Advanced Robotics Trends: Humanoid and Industrial Breakthroughs
Beijing's tech arena recently witnessed mechanical sprinters racing humans through obstacle courses – a vivid showcase of next-gen automation. Over 20 firms displayed humanoid designs at this event, ranging from 5'10" units mimicking adult mobility to compact 2'6" models for precision tasks. These demonstrations reveal strategic progress toward dominating global humanoid production by 2027.
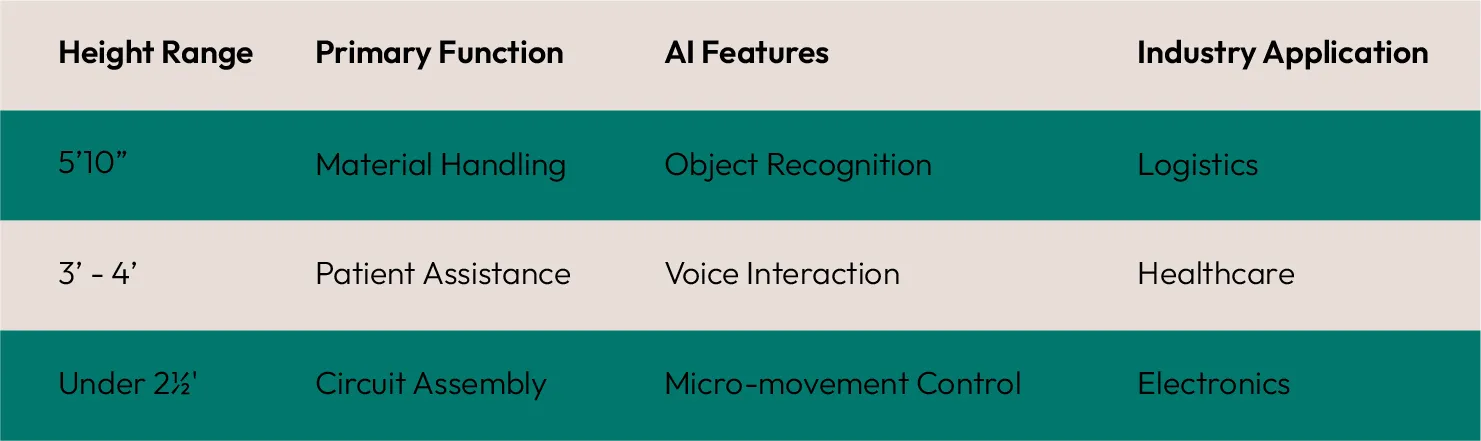
Three breakthroughs drive this evolution. First, machine learning algorithms now process generic data to handle complex tasks – welding robots adapt to new car models in 12 minutes versus 8 hours previously. Second, domestic patent filings for robotic components surged 140% since 2020, reducing foreign reliance. Third, cross-industry applications multiply value: surgical bots perform delicate procedures while educational models teach STEM concepts.
"Our systems learn through shared neural networks," notes a Shanghai-based tech officer. This collaborative intelligence approach lets industrial units optimize processes across factories. Healthcare prototypes already assist with rehabilitation exercises, demonstrating versatility beyond assembly lines.
The roadmap appears clear. With 68% of robotics patents filed domestically and AI integration accelerating, humanoid development enters its commercial phase. Early adopters report 40% efficiency gains in mixed human-machine workflows, suggesting widespread adoption nears feasibility.
Global Impact and Competitor Analysis in the Automation Race
Global manufacturing leaders face unprecedented pressure as automation strategies redefine competitive landscapes. While Japan maintains 45% of industrial exports and Germany excels in precision engineering, the world’s largest consumer of robotic systems operates on an entirely different scale. Over half of all active machines now function within one country’s borders, reshaping supply chains from Detroit to Dortmund.
Cost advantages drive this shift. Domestic firms produce alternatives priced at 80% below Western models, creating what analysts term “the affordability tipping point.” A Shanghai-based automation CEO states: “Our clients choose reliability over perfection – why pay five times more for 10% better performance?” This pricing revolution forces global competitors to rethink R&D budgets and production models.
The U.S. robotics trade deficit hit $1.26 billion in 2022, with exports covering just 28% of import costs. Meanwhile, factories across multiple industries achieve 35% global manufacturing output through scaled automation. Key metrics reveal growth potential:
- Robot density: 322 units per 10,000 workers (Germany: 397)
- Annual installation growth rate: 21% vs. 7% in Japan
- Domestic component production: 65% self-sufficiency
Western nations grapple with fragmented innovation systems, while coordinated policies elsewhere create vertically integrated tech ecosystems. As working-age populations decline globally, automated solutions bridge labor gaps more effectively than offshore outsourcing. The next decade will test whether traditional tech powers can adapt to this redefined playing field.
Conclusion
The automation race has reached a pivotal moment where strategic vision meets industrial necessity. Our analysis reveals a three-part advantage driving progress: relentless market demand, coordinated policy frameworks, and rapid AI integration. These forces position the nation’s tech ecosystem to dominate next-generation value chains.
Demographic shifts will accelerate adoption. With working-age populations declining 4% annually since 2015, smart machines fill critical gaps while boosting output. Factories using adaptive systems report 50% faster production cycles – gains that ripple across global supply networks.
The “robotics+” action plan marks a strategic leap beyond manufacturing. By embedding artificial intelligence into healthcare, logistics, and electronics, this blueprint creates cross-industry synergies. Early adopters already see 40% efficiency improvements in mixed human-machine workflows.
Global competitors face a transformed landscape. As production costs drop 30% through scaled automation, traditional tech leaders must rethink R&D priorities. The convergence of 5G networks and machine learning creates self-optimizing systems that redefine industrial competitiveness.
This revolution transcends factory floors. It represents a fundamental recalibration of economic power structures, with automation serving as both workforce solution and growth catalyst. The coming decade will test whether existing industrial models can adapt to this new reality.
FAQ
Q: What factors have positioned China as a global leader in automation?
A: We attribute this leadership to strategic government policies like "Made in China 2025," heavy investments in R&D, and the rapid scaling of smart manufacturing ecosystems. The nation’s vast industrial base and focus on reducing reliance on manual labor further accelerate adoption rates.
Q: How does government policy shape the development of advanced machinery?
A: Central and local authorities prioritize subsidies, tax incentives, and public-private partnerships to foster innovation. Initiatives targeting AI integration and high-value production chains ensure domestic firms remain competitive in global markets.
Q: What breakthroughs are emerging in human-like automation systems?
A: Innovations include machines capable of complex tasks in healthcare and logistics, powered by enhanced AI and sensor technologies. Collaborative robots (cobots) are also gaining traction, enabling safer human-machine interactions in factories.
Q: How do these advancements affect international manufacturing dynamics?
A: By optimizing production efficiency and reducing costs, China’s progress pressures other nations to accelerate their own automation strategies. Countries like the U.S., Japan, and Germany are investing heavily to maintain their competitive edges.
Q: Can automation address workforce challenges in aging societies?
A: Yes. With a shrinking working-age population, integrating intelligent systems helps sustain productivity. Upskilling programs also prepare workers to manage and operate advanced technologies, balancing economic growth with demographic shifts.
Q: Which industries are adopting these technologies most aggressively?
A: Automotive, electronics, and logistics lead adoption due to high precision demands. Healthcare and agriculture are also embracing specialized systems for tasks like surgery and precision farming, driven by data-driven decision-making.